Fully Stocked Stores Lead to Happy Customers
“Let me check the back,” are words often heard over the past few years, as the item a person has come to purchase appears out of stock. With the rise of labor shortages over the past few years, shelves aren’t always fully stocked like many are used to. One way to alleviate the burden of constantly restocking and allow employees to focus on other tasks is to leverage robots for assistance. At Appen, we provide high-quality computer vision training data that allows these autonomous machines the ability to see what they need to do to restock shelves.
Around the world, robots are being deployed in grocery stores and other retail environments to make restocking the shelves more efficient and cost-effective. They also allow human employees to focus their time on other tasks like customer service and managing orders, and are being considered a solution to labor shortages.
Benefits of Implementing Robots in the Workforce
While for some, robots involvement in daily life may still feel like something out of a futuristic sci-fi movie, it’s very much part of our present. Robots could be coming to a store you shop at in the near future, and they should!
As more autonomous machines are deployed in public spaces, humans are quickly getting used to their presence, and adjusting to a new style of working with their support.
Before they can be deployed, they must be trained. High quality training data is the backbone of a successful deployment of AI and robots. With rigorous AI model training in computer vision and extensive model testing completed at Appen, we ensure all tasks will be carried out safely and efficiently. This will help businesses thrive in the future.
In retail, robots can provide several benefits to customers and business owners, including:
- Robots can work 24 hours a day without being paid, needing a break, or taking sick days. This saves the business money by reducing the cost of human capital.
- Robots will do the job that many humans aren’t applying to, which helps keeps customers in store as the worker shortage is not noticed.
- Robots can take care of dull, repetitive tasks, which frees human employees to take care of human-oriented tasks such as providing high-quality customer service.
- Robots can enhance brand value by showing that a company is committed to innovation and providing the best experience for customers.
- Robots can provide retailers with real-time operational data which can help to streamline processes and limit shortages.
- Shelves will be constantly restocked, which will increase sales as customers will be able to buy all items on their shopping list.
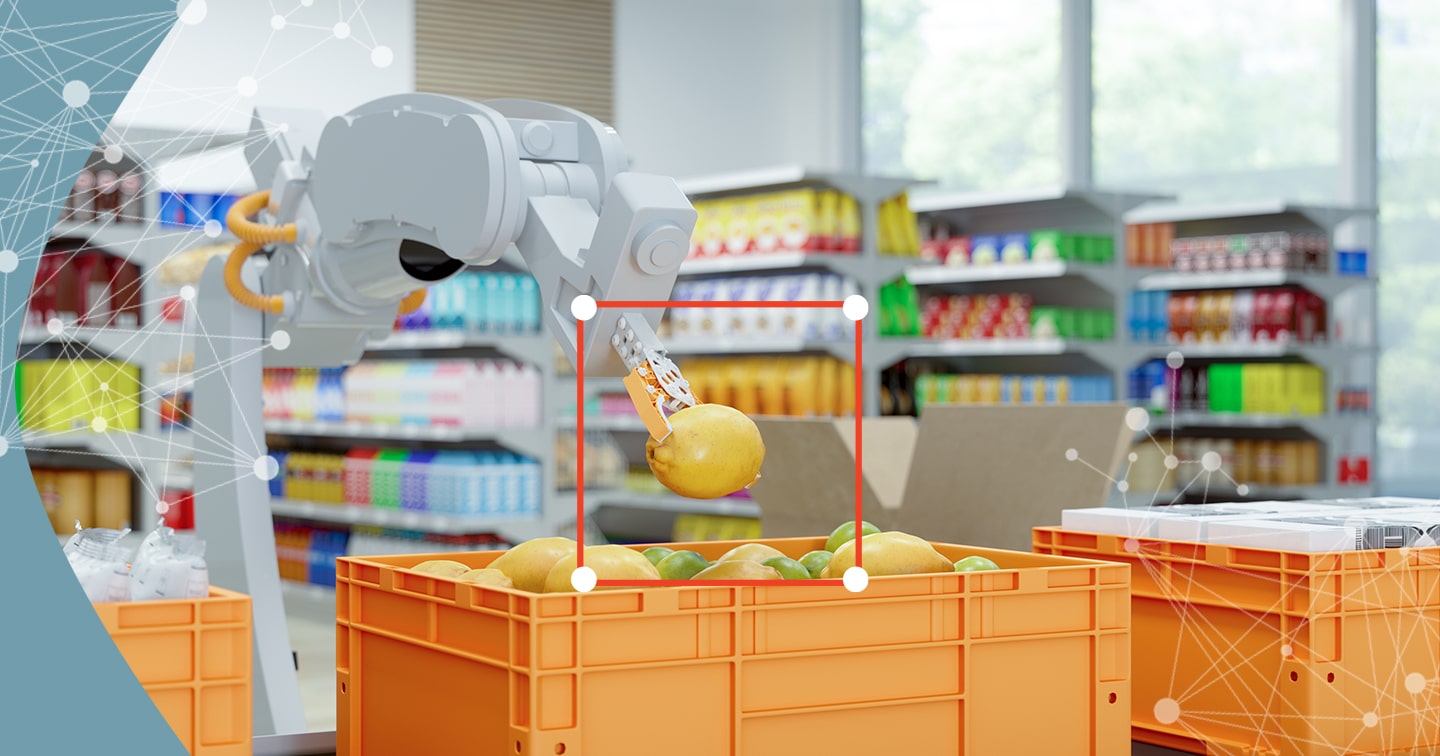
What Do These Robots Do?
If you’ve seen the show Superstore, you’re familiar with robot Glenn in charge of cleaning Cloud 9. Unlike Glenn, robots restocking shelves aren’t capable of cleaning any floors. They’ll be scanning the shelves looking for items low in stock or actively restocking shelves. In the case of Walmart’s short venture into robotics, their machines were designed to simply scan shelves to look for low stock items and were also capable of identifying incorrect pricing. This information was then shared with human workers alerting them to which areas of the store needed to be restocked first. The goal with these machines was to leave no item unstocked, as out of stock shelves lead to a loss in sales when consumers are unable to purchase what they need.
In Japan, their robots are functioning a bit differently and have hands to place products on shelves themselves. The grocery store chain, FamilyMart, has brought them to 300 different locations. Capable of stocking 1,000 bottles and cans a day, or the equivalent of 1-3 hours of human restocking, these robots are off to a bit of a slow start but are invaluable in helping alleviate the burden that labor shortages have left on the business.
In order for robots to perform their designated tasks, they need to be able to see what items are out of stock, this is where computer vision helps give the robots their “eyes” to see. The data supplied is comprised of various images of shelves, display cabinets, end caps, and peg hooks all containing items in a variety of shapes, sizes, and packaging types. Humans annotate this data by drawing bounding boxes over areas in the images where shelves appear out of stock. Once everything is fully annotated, it needs to go through strict quality assurance testing to ensure everything is correct. Once confirmed it’s correct, the machine learning module is trained and is ready for a test run in store.
How Appen Can Help: High-Quality Training Data
With our extensive work in computer vision, we utilize our expertise to provide high-quality training data that can be annotated to easily fit the requirements robots need to properly stock shelves. We even have an extensive Pre-Labeled Dataset (PLD) store that has everything needed to give a jumpstart on trainings. Alternatively, we can source data as needed.
AI isn’t just helping products stay stocked on shelves, it’s also helping more food make it to stores too. Learn how in our article AI Can Help End World Hunger, One Crop at a Time.